HLD900E
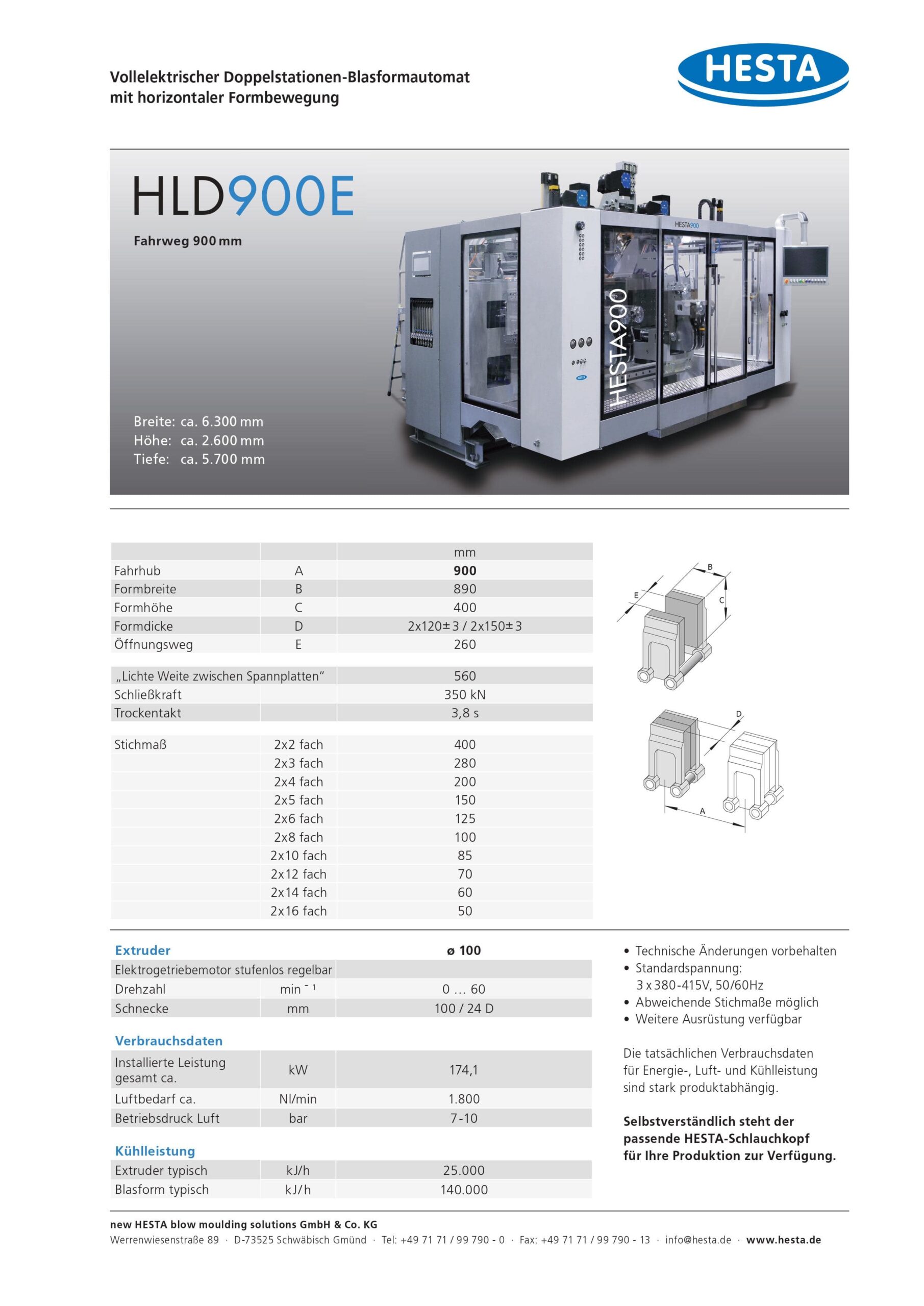
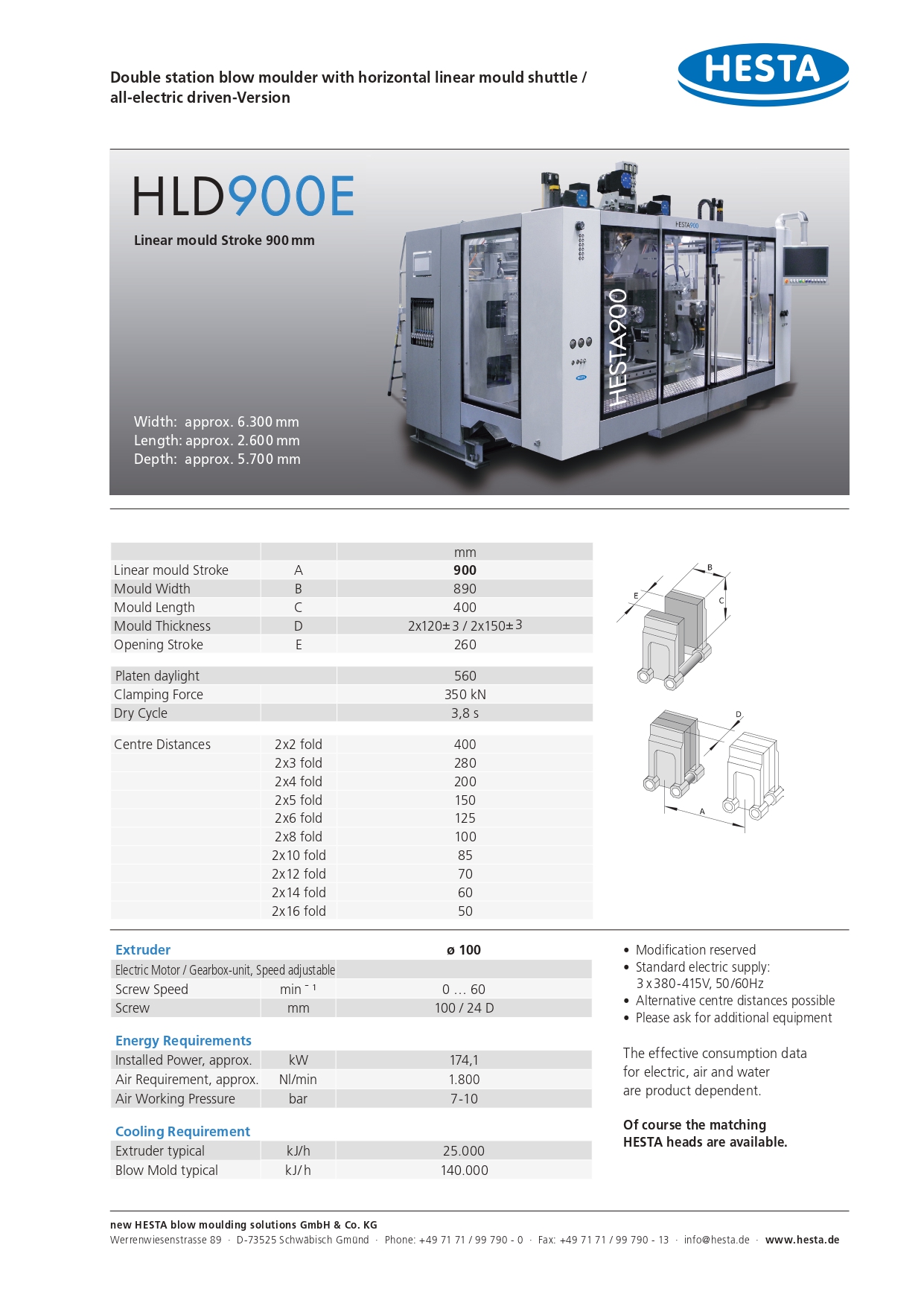
Detailed description
More power for more economy
A blow molding machine with two stations for more efficiency in your production. As a result, the HESTA two-station blow molding machine opens up completely new advantages. Progress that achieves more with less investment, you want maximum bottle production? With the new HESTA blow molding machines of the HL & HLD series, you are well equipped for this job: up to 16 or 2×16 bottles per cycle.
For example, you can run a high-volume job with the highest possible number of nests. Precise, economical and, if required, just-in-time – with minimized inventory. Shortly thereafter, you produce items of larger dimensions with a reduced number of nests. And in between, there are only short set-up times thanks to a quick, easy tool change. This allows you to achieve low unit costs with flexible production and optimized capacity utilization.
The advantages for you:
- High flexibility due to quick tool change: from 2-fold to 16-fold moulds
- High output for large and small batch sizes
- High article quality thanks to new HESTA hose heads
- Energy-saving, high-performance extruder with extruder drive that is unique in the world
- Short changeover times due to directly flanged masks
- Long service life with precise tool guidance due to open locking system with direct
Clamping force application without bending stress on the guide bars
- Safe one-sided application of the tested bottles by means of two-station masks on the mould for the single-station version, left and right for the double-station machine or also directed on one side with a height-adjustable conveyor belt.
- Variable transfer options to the next stations
- Low adjustment effort, as no transport rails are required
- Universally equippable with after-cooling station, circular cutter and bottle tester
- Convenient machine operation
- Low space requirement due to very compact, open design with good accessibility
- Favourable price-performance ratio with high-quality new RESTA quality standard.
To heat up for everything: Our universal extruder
The universal extruder is equipped with interchangeable feed bushings and allows the use of all blowable materials, in powder or granular form, with or without regenerated admixture. Speed control allows the cycle time of the machine to be kept constant. Depending on the material, appropriate screws, with or without mixing part, are used. The unique extruder drive is not only energy-saving, but is also driven by four individual motors. This makes it easy to replace a single engine, as well as emergency operation or operation with reduced power while repairing a single engine.
Our wall thickness control:
The electronic wall thickness adjustment with maintenance-free crank drive is built directly on the extruder, so that it remains on the machine even when the head is changed, which allows for the shortest set-up times and low acquisition costs for an additional hose head. The wall thickness is pre-programmed with 100 points over the entire length of the hose, this can be drawn manually or also drawn, the timing automatically adapts to the cycle time of the blow molding machine.
Our hose head:
A finely graded selection of hose heads is available, in single or multiple versions, mono- or multi-layer designs, web mandrels, quills or spiral designs, for all common nozzle spacings. Our unique Vario heads can be retrofitted by replacing a feed plate from the original mono head to a viewing strip or DeCo2 head. This flexible and cost-effective retrofit is unique in the world.
Tubular knife:
Cold and hot cutting systems are available to cut the hose, these are pneumatically driven, but can also be extended with our unique Electric High-Speed Knife. With a speed of up to 12 m/s, this knife cuts the hose before it notices anything. Thus, the folding of the hose is reduced to a minimum. The portfolio is rounded off by our hose sealing and disconnection device with controlled support air. Immediately after the hose cutting process, the extruder is lifted in the head area by means of a maintenance-free crank drive.
Airy in shape: Our blow heads
With the universal blowing head, economical and time-saving multiple blowing is possible – from 2-fold to 16-fold. The number of individual pre-mountable blowing mandrels depends on the number of moulding nests. Calibration is done electrically with a maintenance-free crank drive with 30kN calibration force. The universal blowing head is safely guided on both sides; The patented calibration pad ensures easy 0-point calibration of the mandrel height to the tee edge in the mold, and reproducible set calibration force for each cycle. The universal blowing head allows 1-fold, up to 16-fold blowing. It can be set up to all available nozzle spacing via position fit grooves. Large cross-sections ensure sufficient air volumes. The blowing mandrels are water-cooled to the tip. It is also possible to provide oblique calibration.
Directional transport:
The blown articles are removed from the blowing mandrel by masks applied directly to the blow mould and transferred to the next station on one level, thus eliminating the need for alignment and set-up and saving extreme set-up times. Double masks can be used to operate an additional follow-up station (e.g. for leak testing). As a result of the transport, the hollow bodies are cooled down well and the output rates are increased. Neck and bottom slugs, as well as handle waste, are removed by pneumatic punching cylinders.
new HESTA's unique tool change concept:
As a novelty, the machine has a patented blow molding and debuting system. With minimal effort and without readjustment during a new set-up process, the essential tool parts such as basform/mask and punches can be replaced. The transfer masks, which are designed for several follow-up stations, are attached directly to the corresponding blow molding halves. The tool parts required for post-treatment fit with the highest precision into the machine-side standardised holders. This makes it possible to replace both the blow molding mask unit and the tool parts in the downstream stations from machine to machine, with minimal effort and without readjustment during a new set-up process. The blowing mandrels are pre-mounted in their mounts so that they can be installed quickly and easily when changing tools. Thanks to this state-of-the-art tool change technology, changeover times are significantly shortened, set-up work and the one-time adjustment of punching tools are simplified, thus increasing the overall degree of utilization. The machine is equipped with the proven 4-circuit cooling system with direct cooling water supply via the clamping plates and O-ring sealing.
Open and close, back and forth: The locking system
The infinitely adjustable clamping force of up to 220 kN / 350 kN is also driven by a maintenance-free crank drive, as well as an adjustable mould opening path. The spars are not subject to bending stress and therefore cause the clamping plates to be guided exactly, and the cooling water is returned by the bars themselves. The patented closing cushion allows you to calibrate the mould thickness of +- 5 mm fully automatically, the closing force can also be optimally adjusted to your article in set-up mode. Human misalignment is excluded with new HESTA. If the machine detects a slight deviation during production, it immediately performs an automatic set-up and adjusts the clamping force. The blowing tool is freely accessible. The lightweight construction results in low masses and thus short cycle times. Two separate cooling circuits are available in each strike plate, whereby the integrated cooling circuit connection through the strike plates not only makes a major contribution to quick change, but also fails connections are excluded. To facilitate tool changes, an additional side door is attached to the protective cover. Here, as with all other components, the latest safety recommendations have been taken into account.
Drive for saving: electric drives and pneumatics
Energy-saving servo drives supply the extrusion unit, the shifting and closing movement as well as the calibration. The associated servo drives from Beckhoff are always of the latest generation and enable cost-effective production by optimally adapting the energy consumption to the utilization of the machine. The pneumatics control the functions of blowing, cooling and transporting. Punching and ejection with proven, mature elements. The standard pneumatic valves are arranged on a central base plate for easy servicing.
Control cabinet & control:
The electrical control cabinet is vibration-damped, easily accessible and easy to service mounted on the machine. The programmable logic controller with front panel meets the highest standards of reproducibility, simple, safe and clear. It allows individual input of all setpoints for the motion sequence, heating and wall thickness regulation as well as the integrated bottle tester. An internal background memory facilitates setpoint optimization. All inputs and fault messages are displayed in plain text. The warning and monitoring systems, which are part of the basic equipment, control the entire machine process. In the basic version, four authorization levels secure unauthorized entries, and personalized login can also be activated as an option. Inputs and all fault messages are recorded for the purpose of tracking processes. For ease of use, two monitor sizes are available, depending on the type of machine. The coloured 12 and 21 inch touch panels are directly connected to the Windows-based modular control system. Any number of setpoint sets can be stored on an internal memory or conveniently via a USB socket on an external memory. This shortens changeover times, especially for small batch sizes, and increases cost-effectiveness. All common languages can be switched quickly and easily. Preparation for online service is a matter of course and easy for us by means of a pre-installed software.
If you want more: The accessories:
- The fully automatic production of wide-mouth containers is carried out either by circular cutters with either electrically or pneumatically actuated, circumferential knife for the removal of the lost head outside the mould in the trimming station, whereby horizontal or vertical cutting is possible.
- The fully integrated bottle tester is used for leak testing and neck checking. This can optionally be extended by a neck passage test. This means that bad items are not handed over in the first place and fall directly onto the slug waste belt. Since 100% tested bottles are transported out of the machine, complaints about leaking bottles are a matter of embarrassment to the end customer.
Get in touch
Do you have any questions?
new HESTA blow moulding solutions GmbH & Co. KG
Address
Werrenwiesenstraße 89
D-73525 Schwäbisch Gmünd
info@hesta.de
support@hesta.de
Telephone & Fax
Phone +49 (0) 71 71 / 99 790 – 0
Fax +49 (0) 71 71 / 99 790 – 13
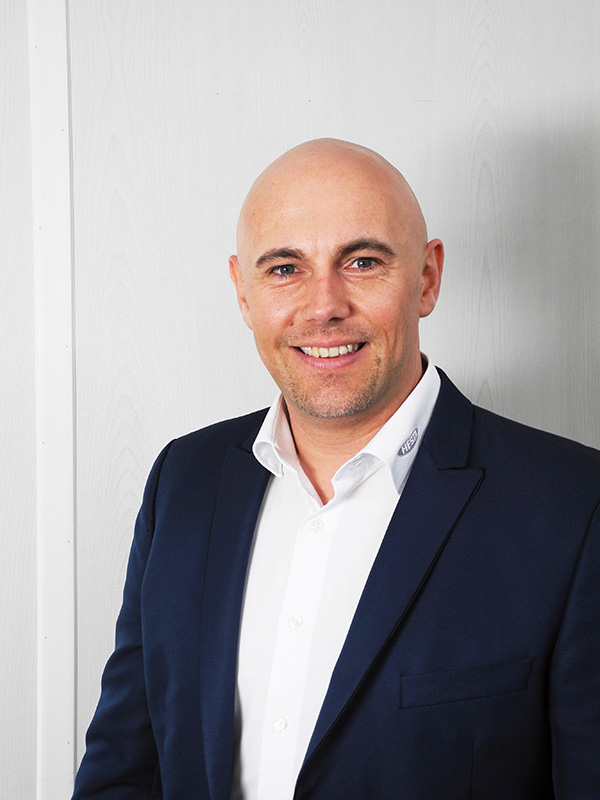
Daniel Knabel
Managing Director, Technical Director, Key Account
Phone +49 (0) 71 71 / 99 790 – 10
knabel[at]hesta.de